
Industrial refrigeration systems are essential to a wide range of industries, including food processing, cold storage, pharmaceuticals, beverage production, petrochemicals, and manufacturing. These complex systems are designed to maintain precise temperature control, ensuring product safety, regulatory compliance, and operational efficiency. The construction of industrial refrigeration systems requires a highly specialized skill set, encompassing engineering expertise, compliance with strict safety standards, and deep industry experience.
At Louis A. Roser Company, headquartered in Salt Lake City, Utah, and serving the greater Western United States including Colorado, Nevada, Oregon, Washington, Montana, Idaho, and California, we understand the nuances of industrial refrigeration construction. With decades of experience, we’ve developed a set of best practices that ensure project success and help our clients avoid common pitfalls.
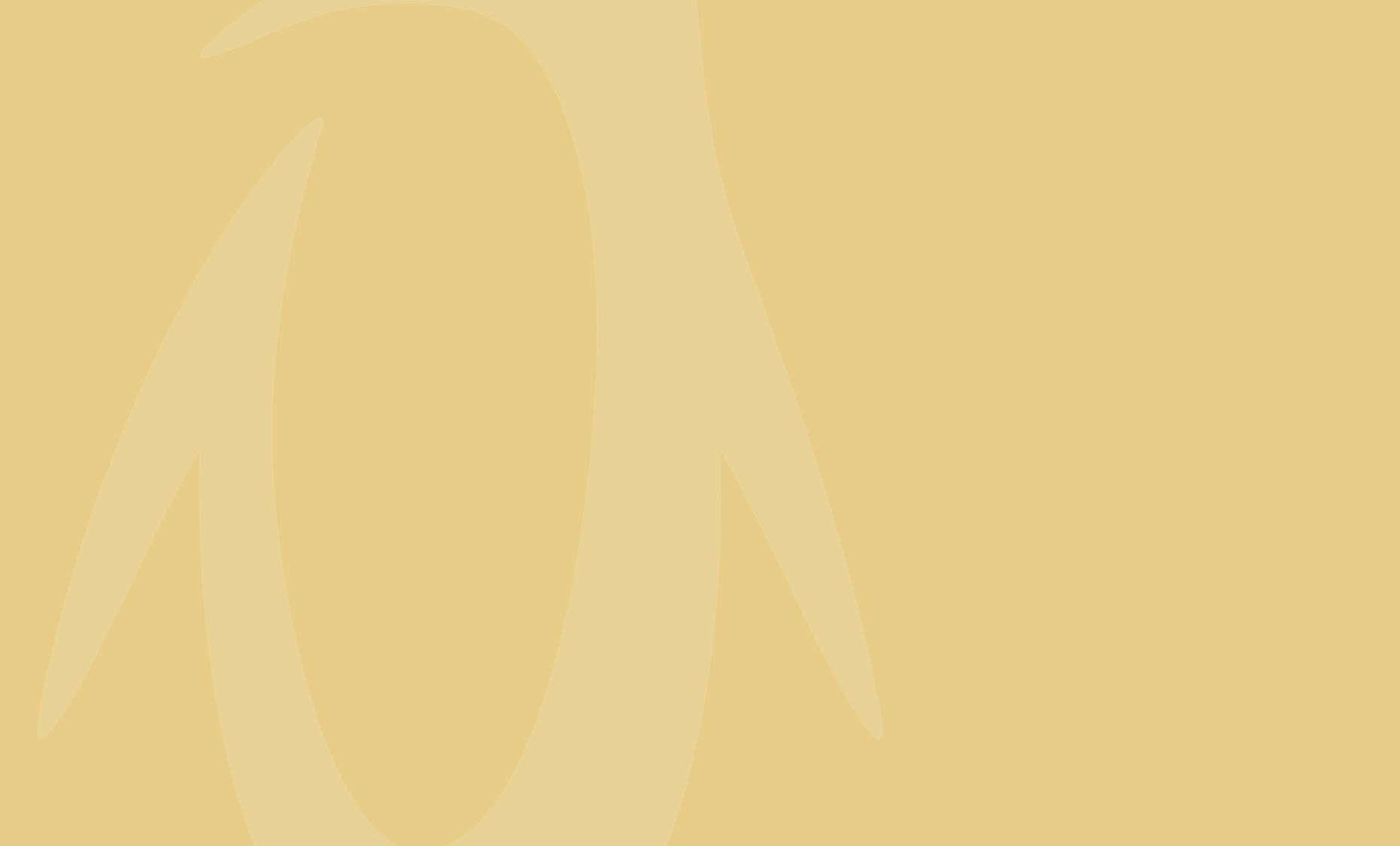
Best Practices in Industrial Refrigeration Construction
1. Comprehensive Planning and Design
Every successful refrigeration construction project starts with detailed planning and design. Skipping or rushing this phase often leads to costly mistakes down the line. Key elements of the planning process include:
- Load Calculations: Precise calculations of cooling and heating loads ensure that the system is designed to meet current and future demands without wasting energy.
- Process Evaluation: Understanding the specific industrial processes helps in designing a system that supports seamless production operations.
- Site Evaluation: Each project location has unique environmental and logistical challenges, such as elevation, ambient temperature variations, and space constraints, that must be factored into the design.
- Regulatory Compliance: The system must adhere to national and local regulations, including EPA, OSHA, ASHRAE, IIAR standards, and state-specific building codes.
- Sustainability Goals: Incorporating sustainability goals into the design, such as refrigerant selection and energy efficiency, can lead to long-term cost savings and environmental benefits.
2. Partnering with Experienced Contractors
Selecting the right contractor can make or break an industrial refrigeration project. A seasoned contractor brings:
- Extensive Industry Experience: Specialized knowledge in ammonia, CO2, and Freon systems, as well as hybrid designs.
- Regulatory Knowledge: Up-to-date understanding of rapidly evolving safety, environmental, and industry standards.
- Proven Project Management: The ability to coordinate complex projects efficiently, minimizing downtime and staying on schedule.
- Skilled Workforce: Certified technicians trained in safety protocols and the latest installation techniques.
At Louis A. Roser Company, we pride ourselves on delivering comprehensive industrial refrigeration solutions from initial concept to final commissioning.
3. Selecting High-Quality Materials and Equipment
Investing in high-quality components ensures the longevity, reliability, and efficiency of the system. Key considerations include:
- Refrigerant Selection: Ammonia (NH3) and carbon dioxide (CO2) are increasingly favored for their environmental benefits and performance.
- Compressors: Modern, high-efficiency compressors reduce energy consumption and maintenance needs.
- Piping and Insulation: Using corrosion-resistant piping and superior insulation materials prevents leaks, improves thermal efficiency, and extends system lifespan.
- Control Systems: Advanced automation and monitoring systems enable real-time performance optimization and predictive maintenance.
4. Energy Efficiency Optimization
Energy consumption is one of the largest operational costs for industrial refrigeration systems. Incorporating energy-efficient design elements offers long-term financial and environmental benefits:
- Variable Frequency Drives (VFDs): Adjust motor speeds based on load demand, reducing energy waste.
- Heat Recovery Systems: Capture waste heat for reuse in other processes, such as water heating or facility heating.
- Advanced Defrost Controls: Optimize defrost cycles to minimize energy use while ensuring consistent performance.
- Real-Time Monitoring: Sophisticated monitoring systems provide insights into system performance, enabling proactive adjustments to maintain peak efficiency.
5. Safety First Approach
Industrial refrigeration systems handle potentially hazardous materials, making safety paramount. A comprehensive safety approach includes:
- Proper Refrigerant Handling: Specialized training for handling and maintaining ammonia, CO2, and other refrigerants.
- Emergency Response Planning: Developing and regularly updating emergency response procedures for potential leaks or equipment failures.
- Employee Training: Continuous training programs ensure all personnel understand and adhere to safety protocols.
- Regular Audits and Inspections: Frequent safety audits identify and address potential hazards before they become serious issues.
6. Rigorous Testing and Commissioning
Commissioning is the final, critical phase before a system becomes fully operational. Proper testing ensures the system operates as intended under real-world conditions:
- Pressure Testing: Verifies system integrity and identifies potential leaks.
- Functional Testing: Confirms that all system components, controls, and safety systems operate correctly.
- Load Testing: Simulates full operational loads to ensure performance and reliability.
- Documentation and Handover: Provides clients with complete operational manuals, training, and maintenance schedules.
Common Pitfalls to Avoid
Despite best intentions, many industrial refrigeration projects encounter challenges that can be avoided with proper planning and execution.
1. Inadequate Site Assessment
Overlooking site-specific factors such as humidity, elevation, and space constraints can lead to design flaws that compromise system efficiency and reliability. Thorough site surveys and environmental analyses are essential to inform design decisions.
2. Cutting Corners on Materials
Attempting to reduce upfront costs by using lower-quality components often leads to higher lifecycle costs due to increased maintenance, reduced efficiency, and shorter system lifespan. Long-term reliability should always take precedence over short-term savings.
3. Ignoring Regulatory Compliance
Regulatory non-compliance can result in fines, project delays, and reputational damage. It is crucial to stay informed about the latest changes in safety, environmental, and industry regulations and ensure full compliance throughout the project.
4. Poor Project Coordination
Lack of communication and coordination among contractors, designers, and facility operators can lead to project delays, cost overruns, and suboptimal system performance. Establishing clear communication protocols and assigning dedicated project managers helps ensure smooth execution.
5. Skipping Preventative Maintenance Planning
A comprehensive preventative maintenance plan should be established before system handover. Regular inspections, equipment servicing, and timely repairs extend system life, maintain efficiency, and prevent costly breakdowns.
6. Underestimating Future Growth
Failing to account for potential facility expansion or production increases can result in a system that quickly becomes undersized. Designing for scalability ensures the refrigeration system can adapt to future needs without requiring major retrofits.
7. Insufficient Operator Training
Well-trained personnel are critical to maintaining safe and efficient operations. Ongoing training programs ensure operators stay current on best practices, safety protocols, and system updates.
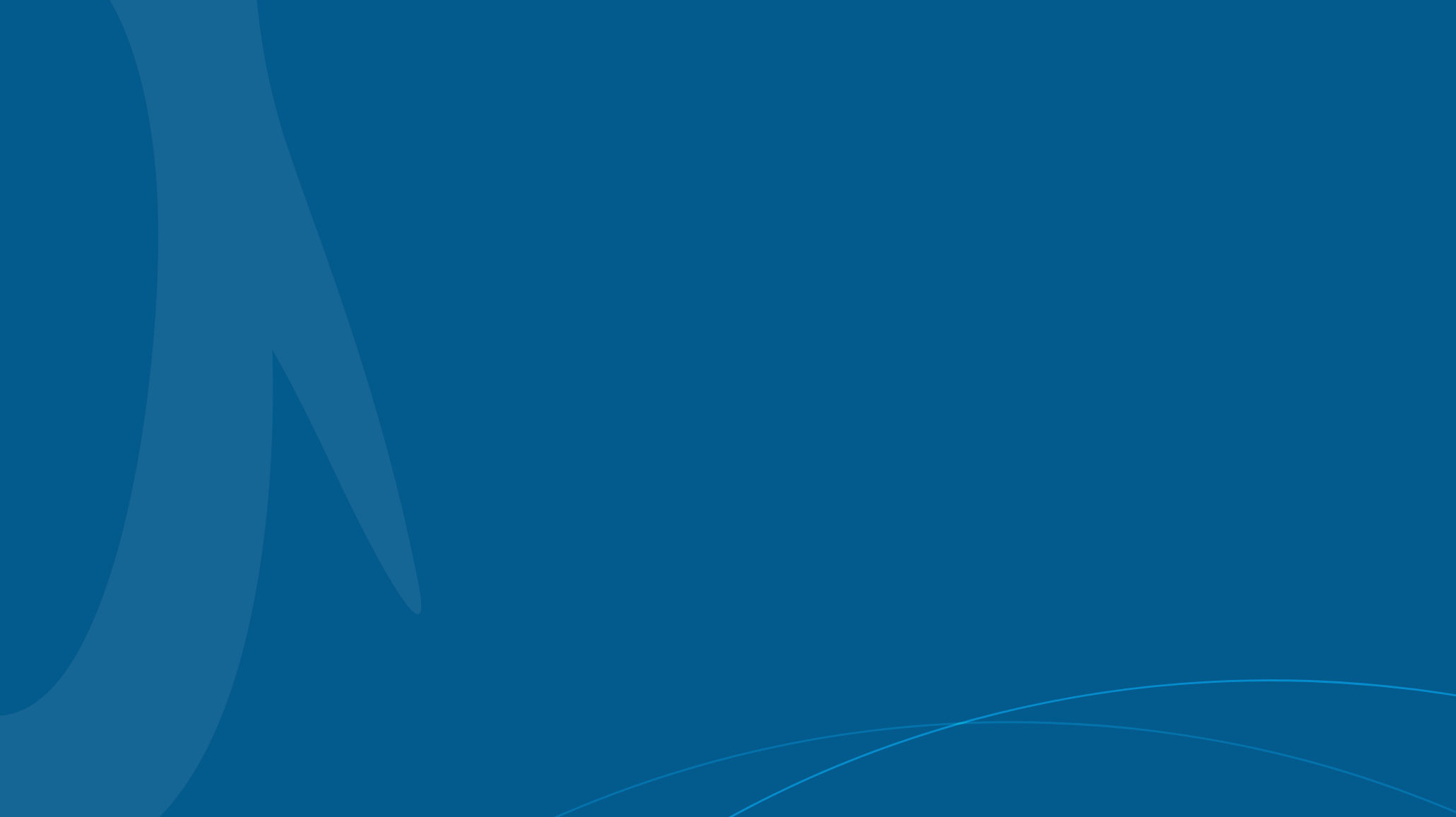
Why Choose Louis A. Roser Company?
With headquarters in Salt Lake City, Utah, and active projects across Idaho, California, Colorado, Nevada, Oregon, Washington, and Montana, Louis A. Roser Company is a trusted leader in industrial refrigeration construction. Our team of engineers, project managers, and certified technicians brings extensive experience across multiple industries, including food processing, pharmaceuticals, cold storage, and manufacturing.
What sets us apart:
- Decades of hands-on experience with complex refrigeration systems
- Full-service capabilities from design to commissioning and ongoing support
- Deep knowledge of regulatory compliance and safety standards
- Customized solutions tailored to each client’s unique operational requirements
- Commitment to energy efficiency, sustainability, and long-term value
By following best practices and avoiding common pitfalls, Louis A. Roser Company delivers refrigeration systems that operate safely, efficiently, and reliably for years to come.